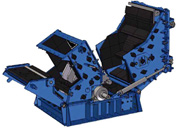
Comminution and classification technologies of iron ore
2022年1月1日 Iron ore operations commonly employ one or more stages of crushing with screening stages incorporated to remove material meeting product size specifications as soon
More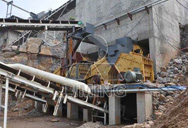
Exploring Low-Grade Iron Ore Beneficiation Techniques: A ... - MDPI
2024年8月2日 Low-grade iron ores require extensive comminution (crushing and grinding), which aids in iron minerals’ liberation from the gangue matter, and ores are usually crushed
More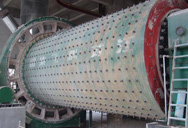
Crushing Plant Design and Layout Considerations - 911 Metallurgist
Ore characteristics are a critical element in both crusher selection and plant design. Dry ores require greater provisions for dust suppression and collection, including dust enclosures
More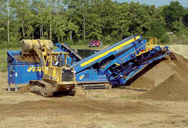
The six main steps of iron ore processing - Multotec
Six steps to process iron ore. 1. Screening We recommend that you begin by screening the iron ore to separate fine particles below the crusher’s CSS before the crushing stage. A static
More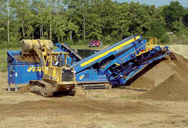
Beneficiation of Iron Ores - IspatGuru
2014年4月3日 For beneficiation of a particular iron ore, the emphasis is normally to develop a cost-effective flow sheet incorporating necessary crushing, grinding, screening, and beneficiating techniques which are
More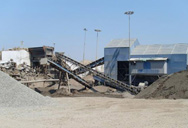
Washing SpringerLink
2023年7月22日 The placers such as gold, platinum, tungsten, and tin, and the highly oxidized and weathered minerals such as lead, copper, iron, and manganese, usually experience
More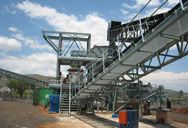
Iron Ore Processing, General - SpringerLink
2022年10月20日 Making iron and steel from iron ore requires a long process of mining, crushing, separating, concentrating, mixing, agglomeration (sintering and pelletizing), and
More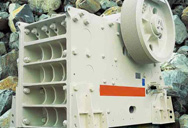
Development of process for beneficiation of low-grade iron ore ...
In preliminary beneficiation studies, the simple techniques of crushing, scrubbing and washing of iron ores met with limited success in the reduc-tion of alumina content due to the finely
More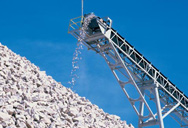
Iron ore washing process and equipment LZZG
The crushing process of iron ore washing plant generally uses feeders, first crushing, second crushing, screening, and fine crushing. In the production of chromite ore, jaw crushers are
More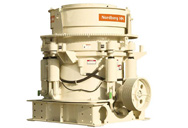
Iron Ore Processing
Iron ore quality in India is deteriorating due to continual increase in consumption of good grade ores. ... screening or wet circuit consisting of crushing, scrubbing , washing and classification [3-4]. ... frequency of 70 strokes per minute with 600 l/min of water flow rate to the jig.
More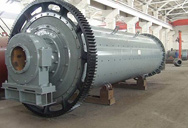
Understanding Iron Ores and Mining of Iron Ore –
2015年4月3日 blasting, crushing, Hematite, Iron ore, magnetite, open pit mining, screening, underground mining, Understanding Iron Ores and Mining of Iron Ore. Iron (Fe) is an abundant and a widely distributed element in the
More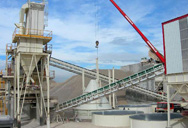
Iron Ore Processing - an overview ScienceDirect Topics
Resource Recovery and Recycling from Metallurgical Wastes. S. Ramachandra Rao, in Waste Management Series, 2006 9.8 Production of Ceramic Tiles from Iron Ore Tailings. Current practice of washing iron ore before it is processed for extractive metallurgical operation results in three products, coarse ore lumps with sizes in the range 10-80 mm, which are directly charged
More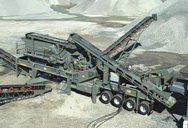
Existing and New Processes for Beneficiation of Indian Iron ores
2020年2月8日 Barsua iron ore mines, a captive iron ore mines of Rourkela Steel Plant, has adopted Remco Jigs for the beneficiation of low-grade iron ore fines at a size range of − 8 + 2 mm. Similarly, a Batac jig has been installed to reduce alumina content from the Noamundi iron ore fines of Tata Steel and the Apic jig used in iron ore mines of South Africa has confirmed
More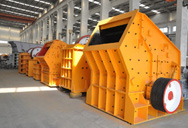
Iron Ore Processing, General - SpringerLink
2022年10月20日 Iron ore handling, which may account for 20–50% of the total delivered cost of raw materials, covers the processes of transportation, storage, feeding, and washing of the ore en route to or during its various stages of treatment in the mill.. Since the physical state of iron ores in situ may range from friable, or even sandy materials, to monolithic deposits with
More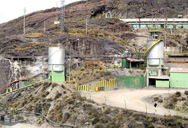
Common Iron Ore Crushing and Screening Process
2021年6月25日 The three-stage closed-circuit process is used as a preparation operation for grinding. Whether it is iron ore mined underground or open-pit, as long as the raw ore contains not high mud content, it can work effectively. Therefore, this process is a crushing process widely used in large and medium-sized iron ore concentrators.
More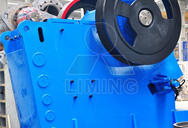
Iron ore crushing equipment and process flow
2022年8月17日 Application field of iron ore crushing material. Iron ore is deeply processed by the crusher and can be widely used in the following industries. 1. Treat pig iron. Pig iron smelting adopts the high-temperature solid-state reduction method, that is, it is smelted under the condition that the furnace temperature is increased to 1150-1300 °C.
More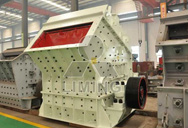
The six main steps of iron ore processing - Multotec
When iron ore is extracted from a mine, it must undergo several processing stages. Six steps to process iron ore. 1. Screening We recommend that you begin by screening the iron ore to separate fine particles below the crusher’s CSS before the crushing stage. A static screen is used to divert the fine particles for crushing.
More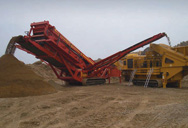
Ore Dressing Methods - 911Metallurgist
2017年4月10日 An ore that is self-fluxing may be of lower grade for direct smelting than one that requires the addition of a large amount of barren flux. On the other hand, a low-grade ore sometimes may be profitably mined and shipped direct because it is high in silica, iron, or lime, or some other fluxing material required by the smelter.
More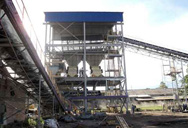
Development of ore sorting and its impact on mineral processing ...
2014年10月15日 The energy costs required to refine metal values contained in ore to concentrates constitute the majority of the cost to produce metals. On average across the mining industry, 44% of the total electricity consumption is dedicated to crushing and milling activities (Fig. 1).Size reduction operations, nearly 150 × 10 9 kW h, are the largest single consumer of
More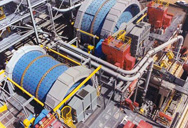
Beneficiation of Iron Ore - 911Metallurgist
2016年5月24日 Beneficiation of Iron Ore and the treatment of magnetic iron taconites, stage grinding and wet magnetic separation is standard practice.This also applies to iron ores of the non-magnetic type which after a reducing roast are amenable to magnetic separation. All such plants are large tonnage operations treating up to 50,000 tons per day and ultimately requiring
More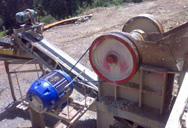
Copper Introduction And Ore Crushing - JXSC Mineral
2024年6月13日 The copper ore powder after flotation is fed into the dryer for drying, and finally, copper concentrate is obtained. Copper Ore Crushing Equipment. Jaw crusher: Used for primary crushing and processing large
More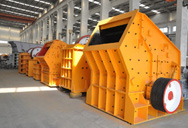
Iron Ore Processing, General - SpringerLink
2022年10月20日 Iron ore handling, which may account for 20–50% of the total delivered cost of raw materials, covers the processes of transportation, storage, feeding, and washing of the ore en route to or during its various stages of treatment in the mill.. Since the physical state of iron ores in situ may range from friable, or even sandy materials, to monolithic deposits with
More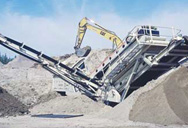
What Are The Equipment Of Chrome Ore Washing Plant?
2024年10月25日 Rotary scrubber. The rotary scrubber is used to clean and screen ore with large mud content but is challenging to wash. The long washing cylinder allows the material to stay inside for a long time, with a vigorous scrubbing ability. The high-pressure washing water washes the inner wall, thoroughly and powerfully dispersing the material completely.
More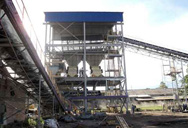
Development of ore sorting and its impact on mineral processing ...
2014年10月15日 The energy costs required to refine metal values contained in ore to concentrates constitute the majority of the cost to produce metals. On average across the mining industry, 44% of the total electricity consumption is dedicated to crushing and milling activities (Fig. 1).Size reduction operations, nearly 150 × 10 9 kW h, are the largest single consumer of
More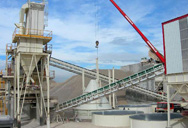
Introduction of Chrome Ore Washing Process and Equipment
2024年8月26日 The chrome ore washing process separates the chrome components from the chrome ore and the veinstone through the steps of crushing, grinding, classifying, gravity sorting and dewatering. The equipment in each step, such as jaw crusher, ball mill, spiral classifier, jigger, shaking table and centrifuge, plays a key role in ensuring the efficiency and effectiveness of
More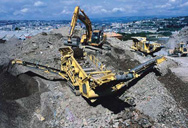
Mineral Processing: Choosing the Efficient Ore Washing Machine
2024年7月23日 1.2. Preventing Equipment Clogging: Ore washing can prevent bins, crushers, and screening equipment from clogging, thereby ensuring smooth operational flow. 1.3. Improving Beneficiation: Ore washing can improve the ore grade and increase recovery rates. For low-grade ores such as manganese, phosphate and iron ore, washing can increase the
More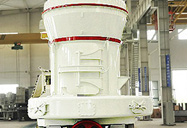
Overview of Ore Washing in the Mineral Processing Industry
2021年2月17日 Ore washing consists of two operations: fragmentation and separation. The crushing operation is mainly to use the washing and soaking effects of water to swell and break the clay, and sometimes it is also supplemented by mechanical impact, stirring, and peeling to accelerate the crushing process.
More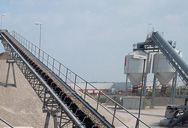
Beneficiation, sintering, and processing of raw materials for the iron ...
BENEFICIATION OF IRON ORES BENEFICIATION of iron ores relates not only to enrichment of the metal content but also to improvements in phy-_ sical characteristics of the ore charged into the blast-furnace. The latter is achieved by crushing, sizing, and agglomeration of resultant fines, etc. It is universally
More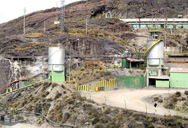
Crushing screening and washing plant for iron ore - CM
22 Apr 2024; Iron ore is one of the most important minerals in the world, and it is used to produce steel. The mining and processing of iron ore is a complex process that involves several steps, including crushing, screening, and washing.
More