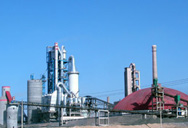
Manufacturing - the cement kiln - Understanding
The original rotary cement kilns were called 'wet process' kilns. In their basic form they were relatively simple compared with modern developments. The raw meal was supplied at ambient temperature in the form of a slurry. A wet
More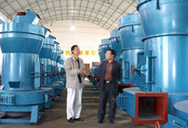
The Cement Plant Operations Handbook - International Cement
Providing a comprehensive guide to the entire cement production process from raw material extraction to the finished product, the industry’s favourite technical reference book is now fully
More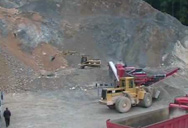
Cement Manufacturing—Technology, Practice, and Development
2021年11月17日 There are four main types of processes used in cement manufacture: Dry Process, Semi-dry Process, Semi-wet Process, and the Wet process. In all these
More
Chapter 4 Cement Manufacturing and Process Control
o the fine powder that we commonly call as cement. The early manufacturing process of cement was through wet process, in which slurry, made of ground ra. material and water, used to
More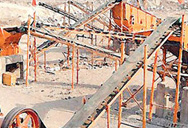
All about the Wet Process of Cement Manufacturing
The wet process of cement manufacturing refers to grinding raw material into slurry after mixing with water and then feeding them into the wet process kiln for drying and calcination and finally forming clinker.
More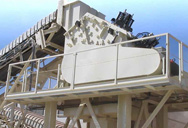
11.6 Portland Cement Manufacturing - US EPA
1971年8月17日 In the wet process, water is added to the raw mill during the grinding of the raw materials in ball or tube mills, thereby producing a pumpable slurry, or slip, of approximately
More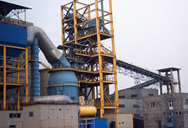
Cement manufacturing process PPT Free Download
2014年6月10日 It is produced through a process involving mixing raw materials, burning in a rotary kiln, and grinding the clinker produced. The manufacturing process can be either dry or wet. Key tests are conducted on cement to
More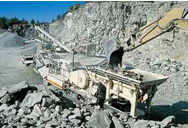
Manufacturing of Portland Cement – Process and
2 天之前 WET Process. In the wet process, first of all, the newly quarried limestone is crushed into smaller pieces. Then in the ball or tube mill, it is mixed with clay or shale with water to form a slurry.
More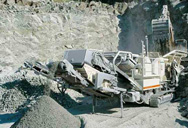
Cement Manufacturing Process: How the Cement is Made?
(II) Wet Process (Old Technology): In the earlier part of the century i.e., from 1913 to 1960, the wet process was used for the manufacture of cement. From 1913 onwards, the cement
More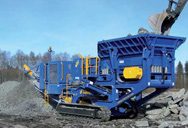
Manufacturing of Cement By Dry and Wet Process
Burning: In this operation, the slurry is directly fed into a long inclined steel cylinder called a Rotary kiln.In this kiln there are 3 different zones shown in fig. below. Cement Manufacturing Process Flow Chart (i) Drying Zones: In the
More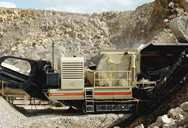
Production Process CEMEX Philippines
Clinker is the intermediate product used in the manufacturing of cement. There are two primary processes used to manufacture clinker: the dry process and the wet process. Our plants use the dry process, which is more energy efficient. In the wet process, the raw materials are mixed with water to form slurry, which is fed into a kiln.
More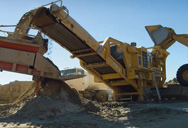
How Is Cement Produced in Cement Plants Cement
The cyclone preheating system Phase IV: Calcination. The calcination is the core phase of the cement making dry process. The calcination of the preheated raw meal takes place in the rotary kiln of the cement plant. The rotary kiln is a
More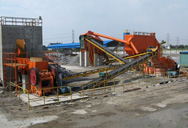
wet process of cement PPT - SlideShare
2018年10月30日 There are two main cement production processes - the wet process, where raw materials are ground into a slurry with water before burning, and the dry process, where they are ground dry. In the wet process, the slurry is sprayed into a rotating kiln to lose moisture and form flakes that are converted into clinker. Read less
More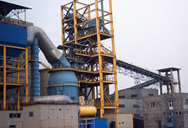
Cement Ball Mill - Cement Grinding Machine - Cement Mill
Cement ball mill is a cement grinding machine used in the cement production line for cement clinker grinding. ... The cement ball mill can be used not only in dry method cement production lines but also in wet method cement production lines. ... Process: Capacity (t/h) Feed size(mm) Rotated speed(r/min) Largest ball charge(t) Rotor power(kW)
More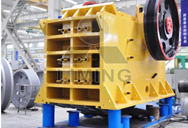
DETAILED WET PROCESS OF CEMENT MANUFACTURING
The kiln must work continuously to ensure a steady regime and uniformity of the clinker. A conventional, larger kiln in a wet process plant produces 3600 tons of clinker per day. Cement manufacturing by wet the process is energy-intensive, so it is uneconomical compared to dry process and semi-dry process.
More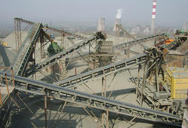
Cement - Extraction, Processing, Manufacturing Britannica
2024年9月26日 Cement - Extraction, Processing, Manufacturing: Raw materials employed in the manufacture of cement are extracted by quarrying in the case of hard rocks such as limestones, slates, and some shales, with the aid of blasting when necessary. Some deposits are mined by underground methods. Softer rocks such as chalk and clay can be dug directly by excavators.
More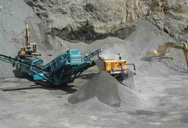
Cement: History, Types, Manufacturing Process - Science Info
2023年8月15日 Wet Process. In the wet process of cement production, calcareous materials, primarily composed of calcium oxide (CaO), undergo a series of steps. ... carefully blended in appropriate ratios and subsequently transformed into a
More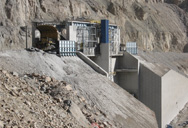
2 Types of Manufacturing of Cement - Wet and Dry Process
The following are the main steps of the dry process of cement manufacturing: Raw Material Preparation. Using crushers, the raw materials, including clay and limestone, are reduced to a size of approximately 25 mm.; According to their chemical composition and quality, they are then stored in various silos or hoppers.
More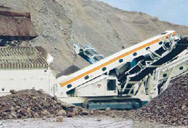
OK™ Raw and Cement Mill
Our best-in-class OK™ Mill is a globally successful vertical roller mill solution for grinding raw material, cement and slag. Its cutting-edge design features consistently deliver the highest quality products with the greatest efficiency. It is affordable to install and cost effective to operate over your cement plant’s lifetime.
More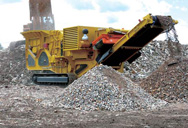
Cement Manufacturing—Technology, Practice, and Development
2021年11月17日 4.3 The Semi-Wet Process. In the semi-wet process, the dewatered slurry from a filter press is used as the feed material. Typically, these filter cakes will have a residual moisture content of 16–21%. This process makes full use of the hot kiln gases and cooler air. Figure 4.8 depicts the semi-wet process.
More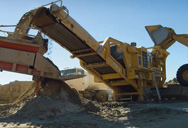
How Is Cement Produced in Cement Plants Cement
The cyclone preheating system Phase IV: Calcination. The calcination is the core phase of the cement making dry process. The calcination of the preheated raw meal takes place in the rotary kiln of the cement plant. The rotary kiln is a
More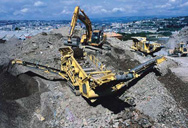
11.6 Portland Cement Manufacturing - US EPA
1971年8月17日 In the wet process and long dry process, all of the pyroprocessing activity occurs in the rotary kiln. Depending on the process type, kilns have length-to-diameter ratios in the range of 15:1 to 40:1. While some wet process kilns may be as long as 210 m (700 ft), many wet process kilns and all dry process kilns are shorter.
More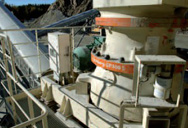
Manufacturing of Cement By Dry and Wet Process - Expert Civil
Burning: In this operation, the slurry is directly fed into a long inclined steel cylinder called a Rotary kiln.In this kiln there are 3 different zones shown in fig. below. Cement Manufacturing Process Flow Chart (i) Drying Zones: In the wet process, the drying zone is comparatively larger than the dry process. It is because the raw material in slurry form is directly fed into the kiln
More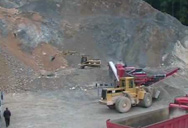
Cement Making Process - Cement Production Process Cement
The comparison data between the wet process cement production line and the new dry process cement production line shows that with the same rotary kiln size (diameter), the production capacity of the cement kiln which adopts the pre-decomposition production process increases more than 200%, the output rises from 27.77kg /m3 to 200.82kg /m3, and the unit heat
More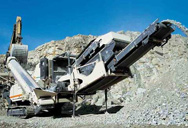
Cement Manufacturing Process - INFINITY FOR CEMENT EQUIPMENT
External Thermal Efficiency is using the recovered heat for other process; Raw mill, Coal Mill and Cement mill drying; Heating and power generation; Speed of Clinker Cooling. Rapid cooling. prevents growth of crystals and its size; gives suitable clinker nodule; solidify the clinker in to glass state; Improve C 3 S and reduce C 2 S leads to ...
More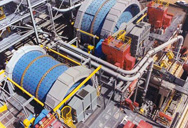
An introduction to Portland Cement Manufacturing
The details of the cement manufacturing process are very broad. No two plants are the same and there may be differences within the same plant in particular since new kiln and their associated equipment can be added to existing ones: for example, wet and dry processes can operate side by side using the same raw materials and producing the same final product and
More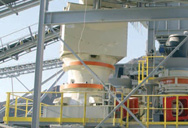
The Cement Manufacturing Process
2017年8月15日 The materials reach temperatures of 2500°F to well above 3000°F in the kiln. Rotary kilns are divided into two groups, dry-process and wet-process, depending on how the raw materials are prepared. In wet-process kilns, raw materials are fed into the kiln as a slurry with a moisture content of 30 to 40 percent.
More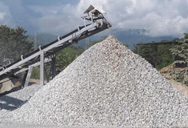
(PDF) Cement Manufacturing - ResearchGate
2015年12月9日 Figure (5): The Wet process of cement (Mahasenan, et.al 2008) ... The second phase is handled in a cem ent grinding mill, which may be located in a different place. to the clinker plant.
More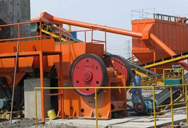
Difference between Wet and Dry process of cement
2018年3月28日 Wet process Mixing of Raw materials in wash mill with 35 to 50% water. Materials exiting the mill are called "slurry" and have flow-ability characteristics. Size of the kiln needed for manufacturing of cement is bigger. Raw material can be mixed easily, so a better homogeneous material can be obtained Fuel consumption is high i.e.,
More